Cubesat-UDAN: CDR erfolgreich abgeschlossen – ein großer Meilenstein für disruptive Antennentechnik Europas
Cubesat-UDAN by HPS: CDR erfolgreich abgeschlossen – ein großer Meilenstein für disruptive Antennentechnik Europas
NewSpace setzt vor allem auf Kleinsatelliten. Deren Effizienz basiert jedoch vor allem auf der Antennenleistung: Je kleiner der Satellit, desto geringer die Antennenleistung und desto teurer ist es, dies am Boden technisch zu kompensieren. Die Lösung von HPS München und seiner rumänischen Tochtergesellschaft in Bukarest: eine Antenne, die außerhalb des Satelliten in Form einer 50 cm hohen konischen Vierfachhelix und einer Bodenebene mit 90 cm Durchmesser aufgestellt werden kann. Sie hat den zusätzlichen Vorteil, dass sie auf noch niedrigere oder höhere Frequenzen als die geplante Bandbreite von 410 bis 460 Mhz skaliert werden kann, aber immer einen Gain von über 10 dBi behält. Zusammengebaut für die Startphase ist das Antennenpaket nur 10x10x15 cm groß.
Die ESA zeigte sich überzeugt und vergab den Entwicklungsauftrag 2018 innerhalb ihres ARTES-Programms an den deutschen Spezialisten für entfaltbare Antennen, die HPS GmbH in München und ihre rumänische Tochter HPS S.R.L., Bukarest. Zwischenzeitlich stellte die Deutsche Raumfahrtagentur im DLR zugunsten der Maximierung effizienter Entwicklung weitere ARTES-Mittel zur Verfügung.
Wir freuen uns, dass auch der nächste große Meilenstein mit Bravour gemeistert wurde: der pünktliche Abschluss der CDR-Phase im März 2025. Es folgt nun die Herstellung des Ingenieurmodells im zweiten und dritten Quartal und anschließend die Testkampagne; der Vertrag endet zum 4. Quartal 2025. Dazu HPS-CEO Ernst K. Pfeiffer: “Mit diesem Projektabschluss wird HPS UDAN´s Reifegrad auf Level TRL 6 und mit einer geplanten In-Orbit-Demonstration (IOD) dann final auf TRL 9 heben. Das bedeutet nicht weniger als: Bahn frei für die Antennentechnik der neuesten Generation auf dem kommerziellen NewSpace-Markt!“
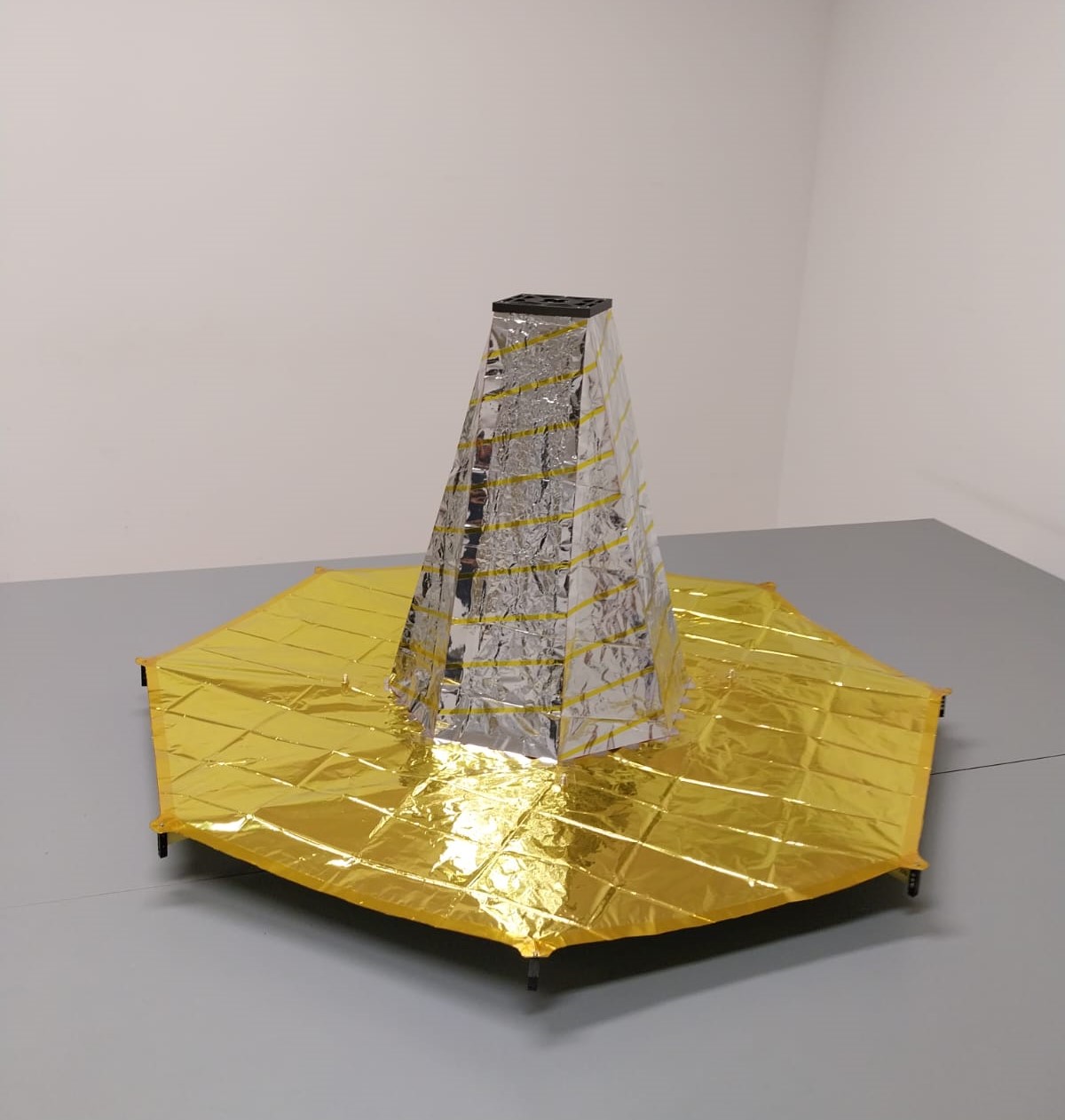
Hochmoderne Antenne für eine der ehrgeizigsten Missionen aller Zeiten
„Wir eröffnen den Wissenschaftlern eine Schatztruhe an Informationen“, sagte Esa-Wissenschaftsdirektorin Carole Mundell. Clotilde Laigle vom „Euclid“-Konsortium bezeichnete die neu gewonnene Sonde von EUCLID als eine „Goldmine an Daten“.
HPS, führender Anbieter fortschrittlicher Antennen- und Reflektortechnologien, beglückwünscht die Europäische Weltraumorganisation ESA zu diesem bemerkenswerten Fortschritt im Projekt EUCLID (European Space Agency’s Cosmic Vision: Euclid), das darauf abzielt, die Geheimnisse des dunklen Universums zu entschlüsseln und Erkenntnisse über die Natur der dunklen Materie und der dunklen Energie zu gewinnen.
Die von HPS im Rahmen des TAS-Vertrages entwickelte Antenna Reflector Assembly (ARA) von EUCLID stellt einen bedeutenden Fortschritt in der Weltraumkommunikationstechnologie dar. Ihr innovatives Design und ihre fortschrittlichen Eigenschaften machen sie zur idealen Wahl für die Mission, da sie eine Hochgeschwindigkeitsdatenübertragung und einen Hochgeschwindigkeitsdatenempfang vom Raumfahrzeug zur Erde und zurück ermöglicht.
„Wir freuen uns sehr, einen wichtigen Beitrag zur Euclid-Mission leisten zu können“, sagt Ernst K. Pfeiffer, CEO von HPS. „Unsere Spitzentechnologie ermöglicht eine nahtlose Kommunikation zwischen der Raumsonde und den Bodenstationen und erlaubt es den Wissenschaftlern, uns auf der Erde all die Geheimnisse des dunklen Universums zu entschlüsseln.“
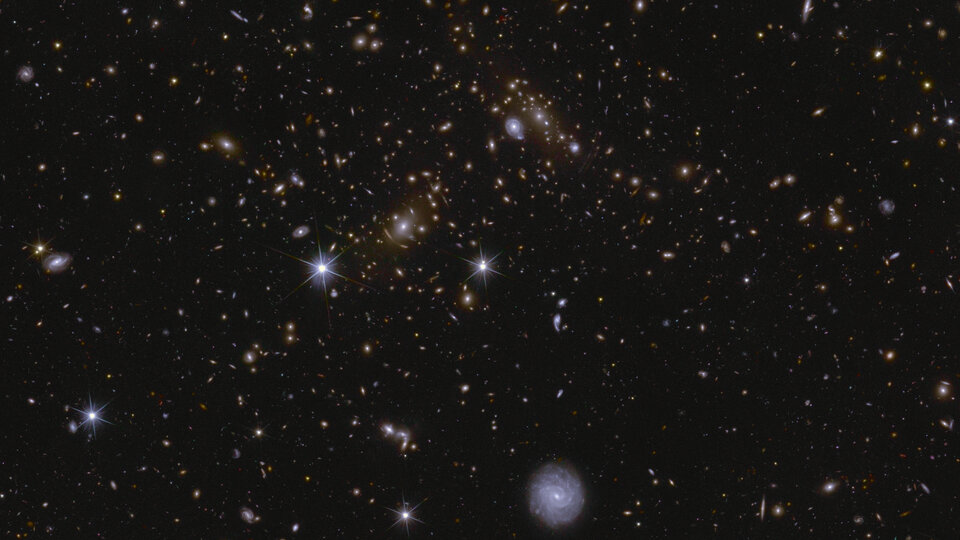
Bild von ESA
Weltraumpremiere auch für die neuartige Reflektorantenne BANT-1 von HPS
Am 14.01.2025 startete an Bord einer Falcon 9 – Rideshare-Mission Transporter-12 mit „SIGI“ der erste Satellit aus der NextSpace-Schmiede Reflex Aerospace, Berlin/München. „NextSpace“ ist der exklusiv für Reflex geschützte Begriff für die neue Schnelligkeit in Entwicklung, Fertigung und Bereitstellung von Raumfahrttechnik, gepaart mit innovativer Vielseitigkeit als Leitmotiv für die Leistung des Produktes.
Das galt in hohem Maße auch für ein wesentliches nicht bei Reflex gefertigtes Element des Satelliten: die von HPS entwickelte Breitband-primäre Reflektorantenne des Raumfahrt-Mittelständlers HPS GmbH (München, Deutschland) mit einer Hohlraum-Spiralantenne als axialer Einspeisung für eine große Bandbreite sowie beträchtlichen Gain – und das Ganze von der Bestellung zur Ablieferung in nur 12 Monaten.
HPS gratuliert Reflex Aerospace herzlich zum ersten Start eines seiner Produkte und freut sich auf die Zusammenarbeit bei den nun bevorstehenden weiteren NextSpace-Herausforderungen in den Weiten des Weltraums.
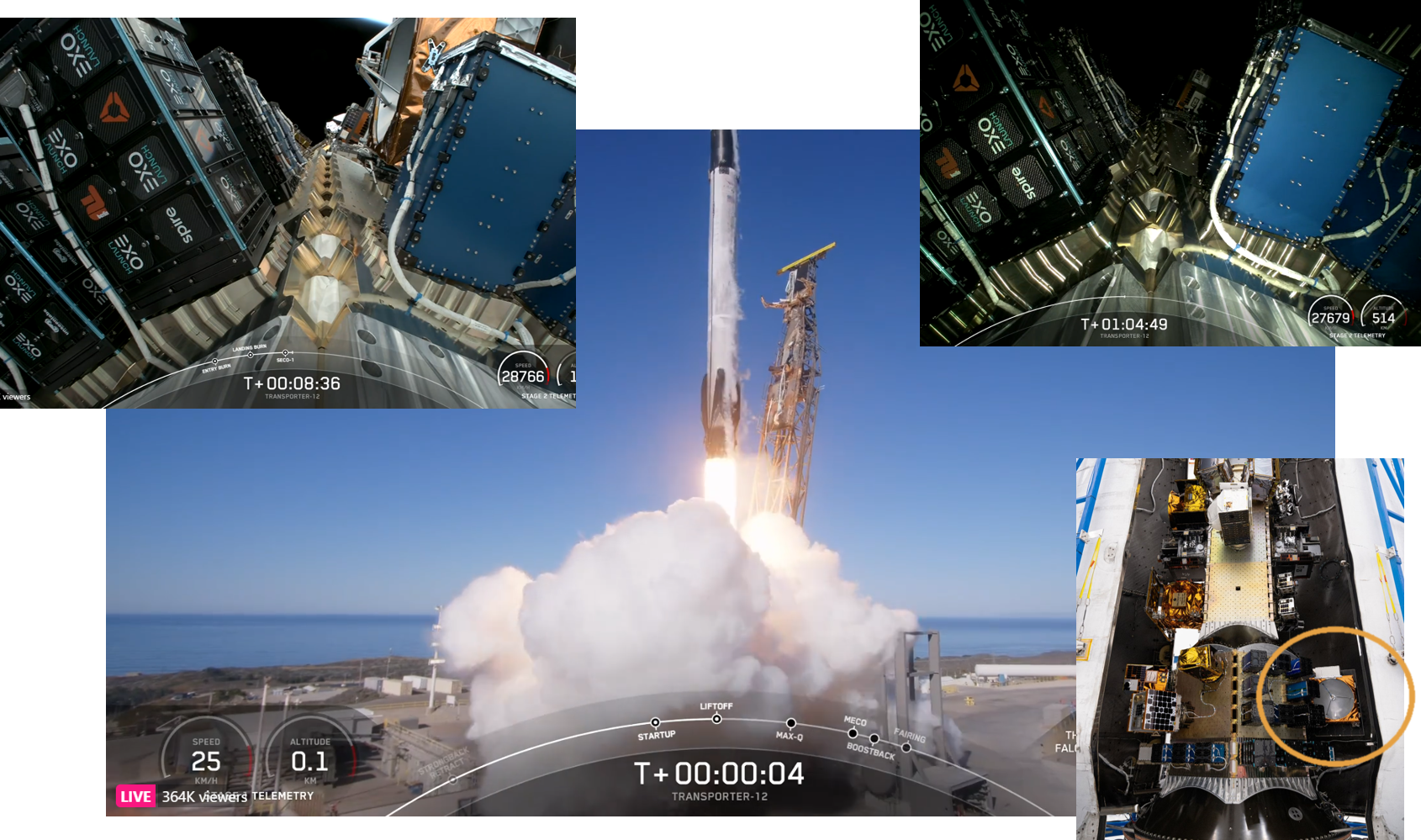
Pictures by SpaceX
Antennenspezialist HPS erobert mit Verifizierung innovativer 3D-Fertigung Neuland der RF-Anwendungen
Mittlerweile sind sich auch ehemals sehr skeptische Auguren der Raumfahrt einig, wesentlichen Einfluss auf den Verlauf der künftigen Entwicklung von anwendbaren Technologien wird vor allem die Fähigkeit zur weitgehend automatisierten Produktion von Leichtgewichtbauteilen in Serie bei gleichzeitiger Minimierung von Rohstoffen und höchster Zuverlässigkeit haben.
Zentrale Voraussetzung für die Umsetzung solcher Visionen ist jedoch weiterhin eine sehr klassische Step-by-Step-Verifizierung, in diesem Falle zweier von den HPS-Ingenieuren ausgewählter Materialien anhand der neuen ESA-Norm ECSS-Q-ST-70-80C.
Die europäische und die deutsche Raumfahrtagentur haben angesichts des Zukunftspotentials solcher Technologie ein vorrangiges Interesse am Erfolg der Forschung bei HPS und stellten die GSTP-Finanzierung für das Projekt 3DPAN2 bereit: „3D-Printed Antenna 2“ ist ein Nachfolger-Projekt des vor 5 Jahren abgeschlossenen Projektes 3DPAN, mit dem zunächst die prinzipielle Machbarkeit von 3D-gedruckten RF-Bauteilen gezeigt wurde.
Produktziel war eine extrem leichte X-Band Antenne mit einem Durchmesser von ~30cm für den Daten-Downlink von Erdbeobachtungssatelliten. Hergestellt wurde sie schließlich aus der Aluminium-Legierung SCALMALLOY beim Sub-Contractor APWORKS GmbH in Ottobrunn. Zudem wurde für ausklappbare Antennen ein filigranes Feed Support Bracket aus Titan vom langjährigen HPS-Vertrauenspartner, dem Fraunhofer-Institut für Werkstoff- und Strahltechnik IWS, Dresden, als Subunternehmen gefertigt.
Die jeweiligen Designs und FE-Analysen, sowie deren iterative Optimierung wurde derweil durch HPS in München selbst durchgeführt.
Die abschließenden Tests lieferten über alle Erwartungen positive Ergebnisse. Dies galt insbesondere für die RF-Performanz der X-Band Antenne in der Compensated Compact Range (Munich University of Applied Science MUAS). Auch die Beständigkeit gegen Vibration (Sinus + Random) wurde für beide Demonstratoren bei der Firma SGS GmbH, Geretsried, erfolgreich nachgewiesen: auch hier lief alles ohne Komplikationen ab, also vor allem ohne Beschädigungen oder Verformungen. Selbst ein abschließender TVAC-Test (10 Zyklen zwischen +120°C und – 120°C) zeigte keinerlei Risse oder Verformungen an den Demonstratoren.
Das Fazit des Projektes formulierte Olaf Stolz als zuständiger Projektmanager von HPS so: „Die Ziele der Verifikationsprozesse konnten ohne Einschränkungen umgesetzt werden: die additiv gefertigten Demonstratoren waren 20% bzw. 25% leichter als entsprechende konventionell gefertigte Bauteile – ein bekanntermaßen enormer Vorteil in der Raumfahrt. Dabei kam es zu keinerlei Einschränkungen der Qualifizierung für Raumfahrtanwendungen. Unser Dank gilt den Kooperationspartnern, besonders Frau Dr. Samira Gruber (Fraunhofer IWS) und Herrn Nicklas Schwab (APWORKS) für die extrem gute und erfolgreiche Zusammenarbeit in dem Projekt, sowie bei der ESA, namentlich Frau Isabel Olaya Leon, Technical Officer des Projektes 3DPAN2“.
HPS-CEO Ernst K. Pfeiffer freut sich: „Es ist fantastisch, schon jetzt werden bei uns in aktuell laufenden Flugprojekten 3D-Druck-Bauteile mit den Technologieergebnissen des ESA-GSTP-Programmes umgesetzt. Ein von uns vor 8 Jahren anvisiertes und für den Zukunftsmarkt essentielles Ziel ist jetzt damit erreicht.“
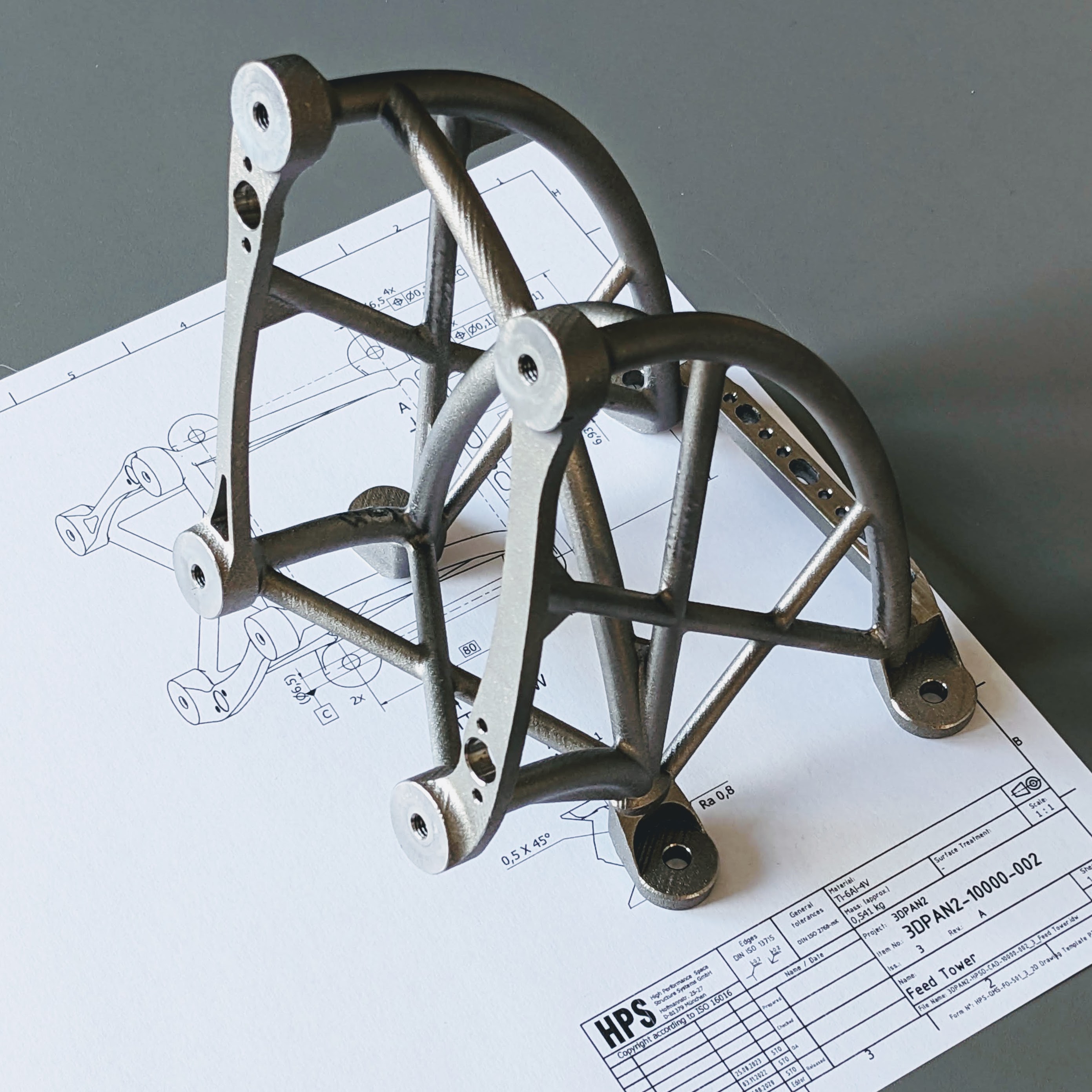
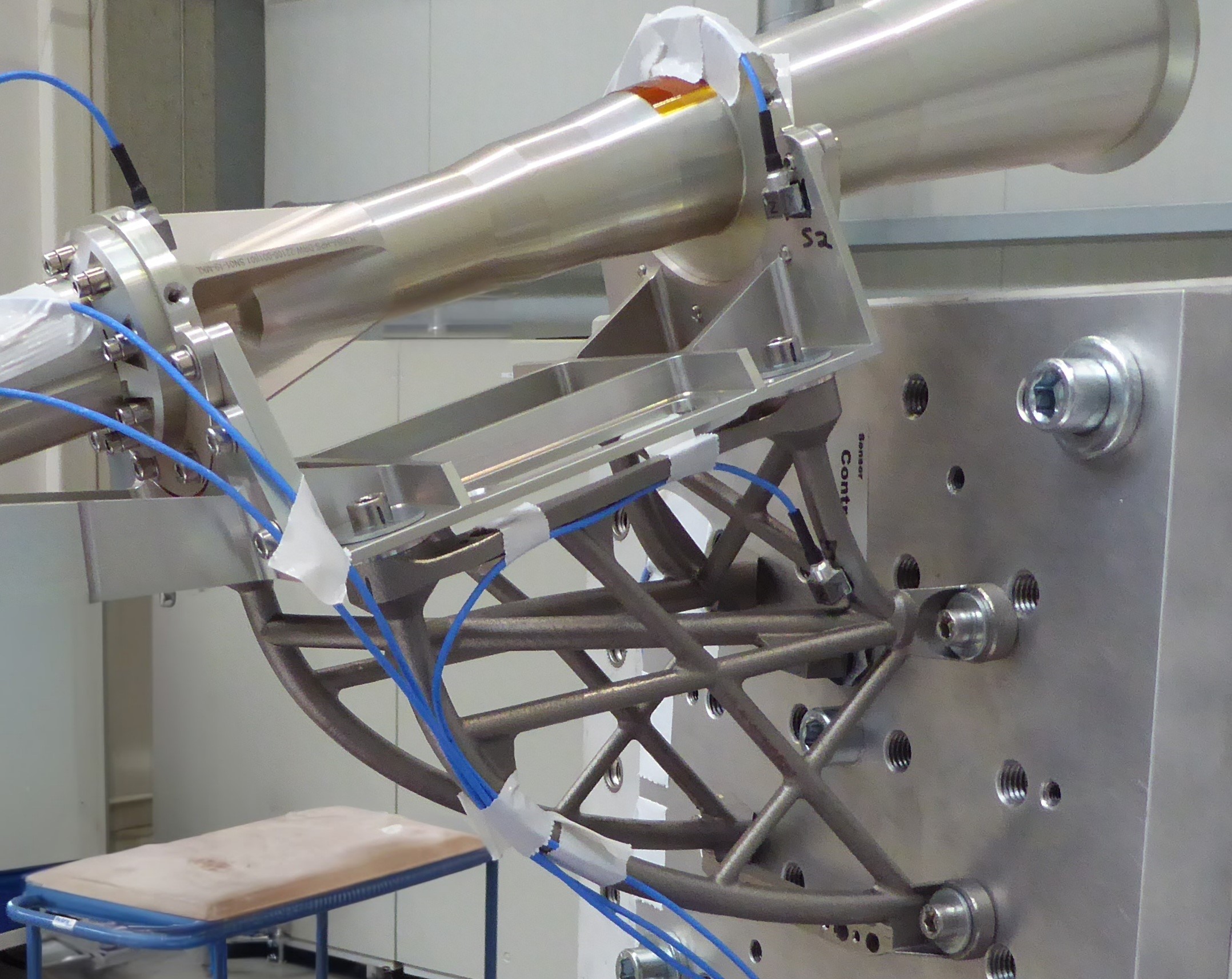
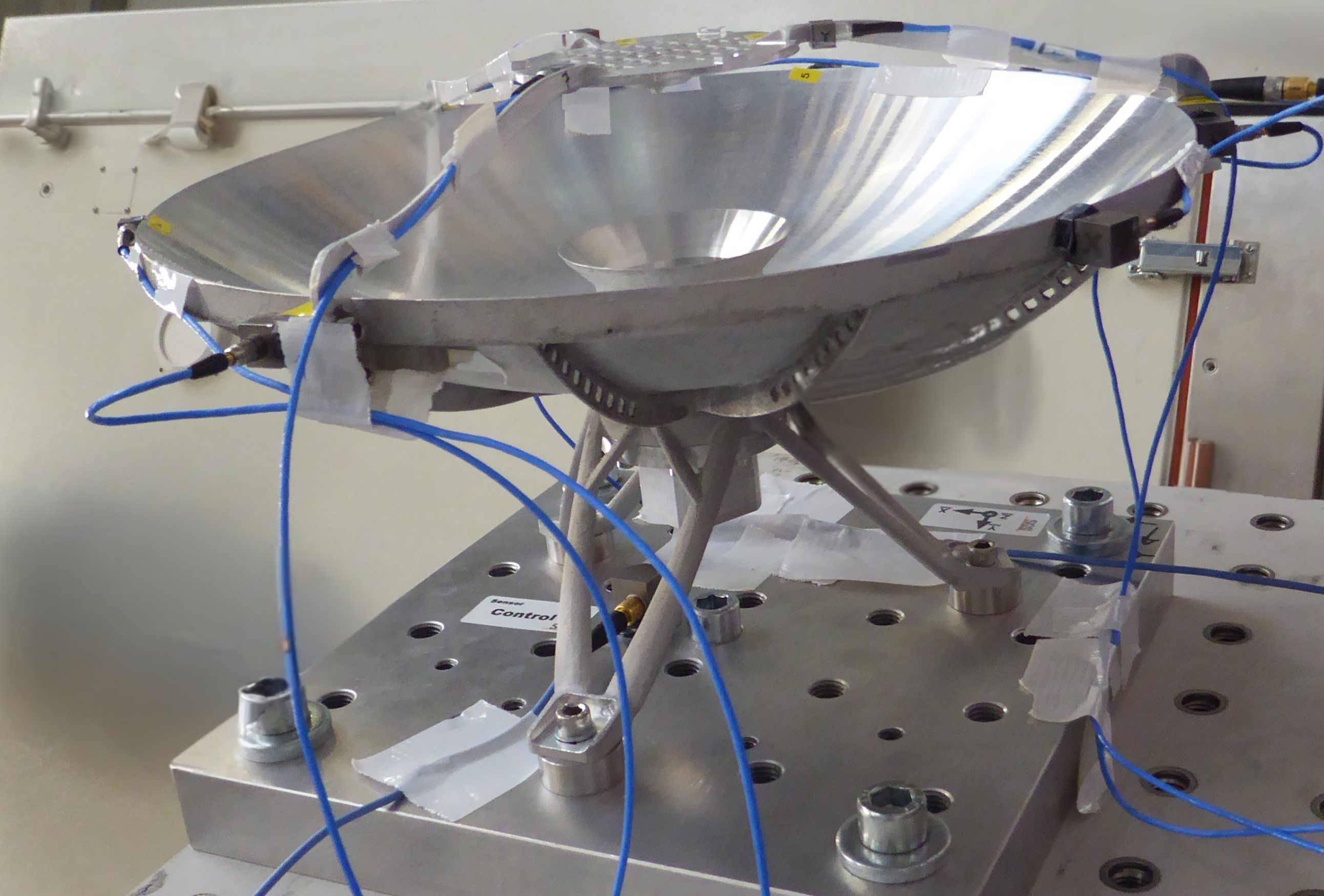
Antennenfertigung in Serie
Die Münchner Raumfahrtschmiede HPS ist seit über 20 Jahren dafür bekannt, wo immer möglich neue Wege zu gehen und mit Innovationen aller Art eine immer festere Brücke zwischen ClassicSpace und CommercialSpace zu etablieren. Dies gilt für Produkte wie beispielsweise entfaltbare Antennen aller Größen bis hin zu Prozessen wie etwa zur Serienfertigung der Produktfamilie von Deorbit-Segelmodulen (ADEO).
Mit der Umsetzung einer weiteren Prozessinnovation realisiert HPS nun auch im Antennenbereich neue Effizienzhorizonte; denn ein kommerzieller Kunde hat es eilig: über 20 Breitband Antennen werden benötigt, und das in einem Zeitraum von nur 12 Monaten, Start JETZT. Zwar ist HPS schon aus einer Vielzahl von erfolgreich erfüllten Antennenaufträgen – ob nun aus dem institutionellen oder dem kommerziellen Bereich – für die von den Kunden geschätzte Routine der Qualitätsherstellung auf gleichbleibend hohem Niveau bekannt. Doch nun läutet das Unternehmen mit der anlaufenden Kleinserienfertigung eine weitere
Entwicklungsstufe ein, die Qualitätsmerkmale von konventioneller und neuer Raumfahrt miteinander zu etwas Neuem und dabei noch Besserem zu verschmelzen. Und das trotz allen Hochdrucks mit der Kraft, die aus der Ruhe kommt.
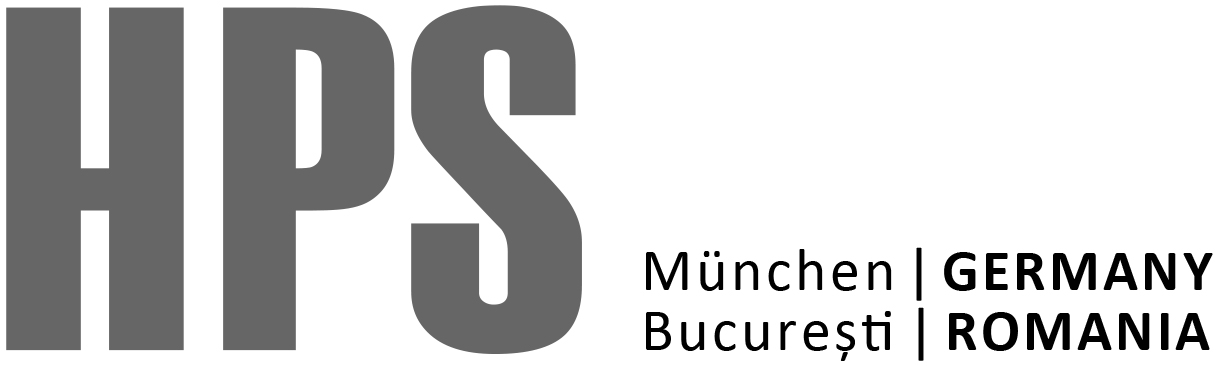