Pushing the limits of what’s possible in CubeSat technology – for science, for Earth, for the future
We are thrilled to announce that HPS GmbH has been awarded a new Technology Activity by the European Space Agency (ESA)! The contract signature has been taken place on 08.04.2025.
In this groundbreaking GSTP-project, we will develop a cutting-edge CubeSat deployable ArrayAntenna in collaboration with our esteemed partners at Fraunhofer-Gesellschaft (IIS, Germany). This innovative technology, known as MANT (Miniaturized Deployable Antenna for Small and Nanosatellites), will reach TRL6 by the end of the project, marking a significant advancement for the capabilities of small and nanosatellites focussed to civil Earth Observation applications, which always would enable also “Dual Use”. The project is fully funded with a budget of 750,000 euros and will run for two years.
We are excited to contribute to the next generation of satellite technology, advancing small satellite communication with more efficient, compact, and powerful solutions. Stay tuned for updates such as for detailed geometries (in stowed configuration: less than 1U), frequencies and interfaces, as we never stop working towards transforming space technology!
Next Milestone: Requirements Review by end of May.
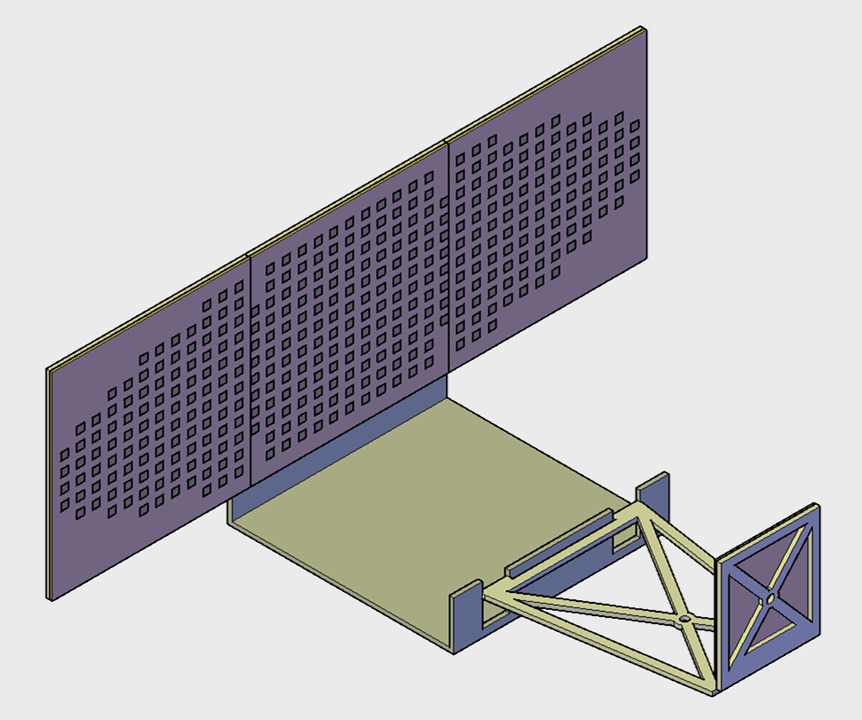
Cubesat-UDAN by HPS: CDR successfully completed – a major milestone for Europe’s disruptive antenna technology
Cubesat-UDAN: CDR successfully completed – a major milestone for Europe’s disruptive antenna technology
NewSpace relies primarily on small satellites. However, their efficiency is primarily based on antenna performance: the smaller the satellite, the lower the antenna performance and the more expensive it is to technically compensate for this on the ground. The solution from HPS Munich and its Romanian subsidiary in Bucharest: an antenna that can be deployed outside the satellite in the form of a 50 cm high conical quadruple helix and 90 cm diameter ground plane with the additional advantage that it can be scaled to even lower or higher frequencies than the planned bandwidth of between 410 and 460 Mhz but always keeping a gain above 10 dBi. Stowed together for the launch phase, the antenna package is only 10x10x15 cm in size.
ESA was convinced and awarded the development contract in 2018 within its ARTES program to the German specialist for deployable antennas, HPS GmbH in Munich and its Romanian subsidiary HPS S.R.L., Bucharest. In the meantime, the German Space Agency at DLR has provided further ARTES funding to maximize efficient development.
We are delighted that the next major milestone has also been passed with flying colors: the punctual completion of the CDR phase in March 2025. This will now be followed by the production of the engineering model in the second and third quarters and then the test campaign; the contract ends in the fourth quarter of 2025. HPS CEO Ernst K. Pfeiffer comments “With this project completion, HPS will raise UDAN’s maturity level to TRL 6 and then finally to TRL 9 with a planned in-orbit demonstration (IOD). This means nothing less than clear the way for the latest generation of antenna technology on the commercial NewSpace market!”
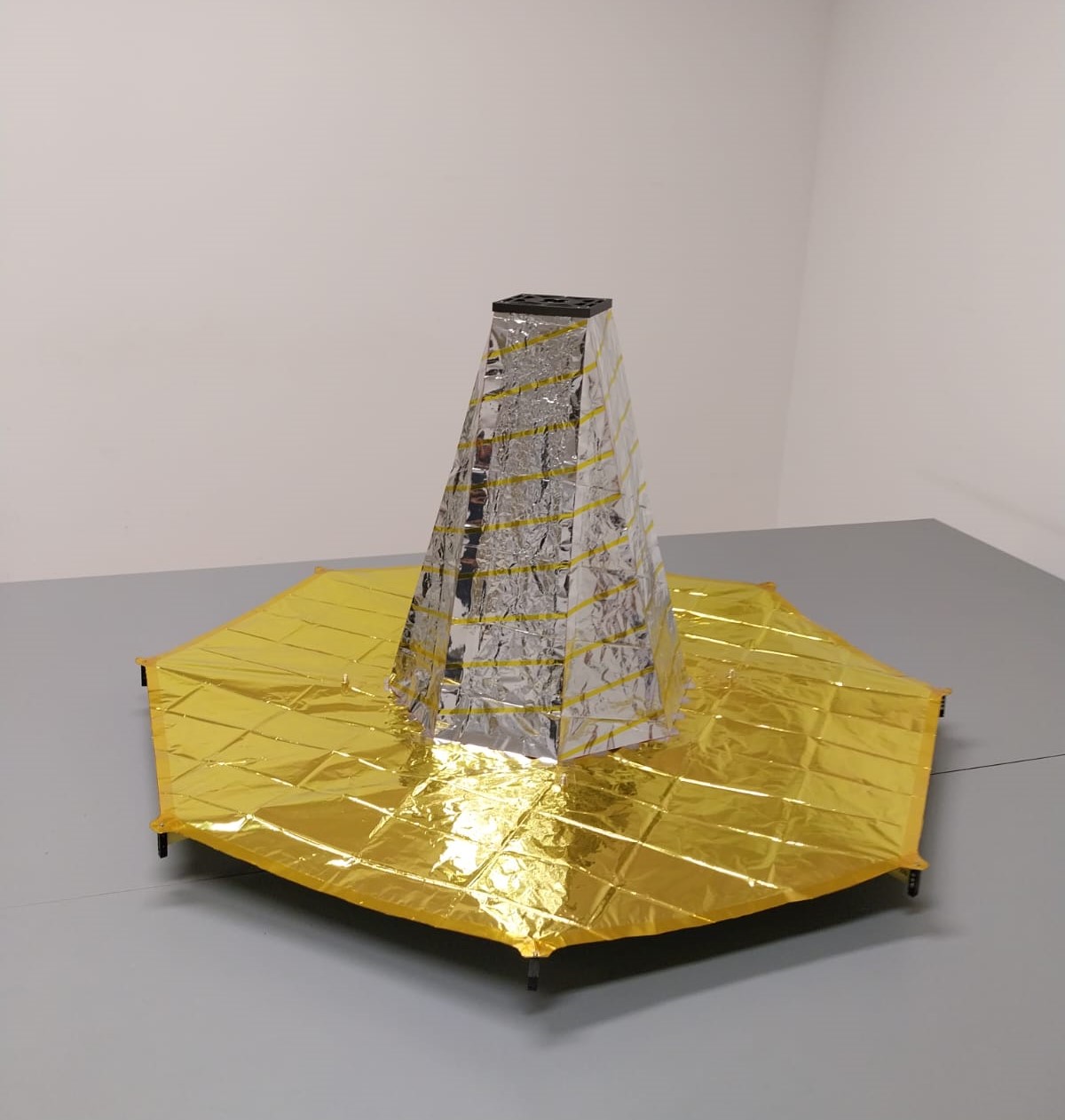
State-of-the-art antenna serving one of the most ambitious missions ever
“We are opening up a treasure trove of information for scientists,” said Esa Science Director Carole Mundell. Clotilde Laigle from the “Euclid” consortium described the newly won probe of EUCLID as a “gold mine of data”.
HPS, leading provider of advanced antenna- and reflector-technologies, applauds the European Space Agency ESA to this remarkable progress in the project EUCLID (European Space Agency’s Cosmic Vision: Euclid) which aims to unravel the mysteries of the dark universe and gain insights into the nature of dark matter and dark energy.
EUCLID´s Antenna Reflector Assembly (ARA)” developed by HPS under TAS-contract represents a significant advancement in space communication technology. Its innovative design and advanced features make it an ideal choice for the mission, enabling high-speed data transmission and reception from the spacecraft to Earth and back.
“We are thrilled to contribute significantly to the Euclid mission,” says Ernst K. Pfeiffer, CEO of HPS. “Our cutting-edge technology facilitates seamless communication between the spacecraft and ground stations and allows scientists to unlock and reveal to us on Earth all those mysteries of the dark universe.”
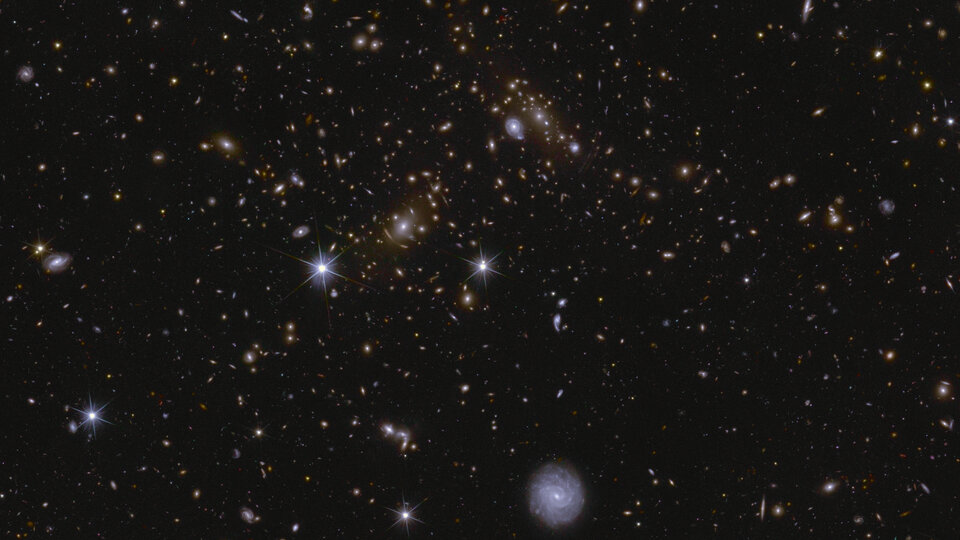
Picture by ESA
Space premiere also for the innovative BANT-1 reflector antenna from HPS
On January 14, 2025, “SIGI”, the first satellite from the NextSpace company Reflex Aerospace, Berlin/Munich, was launched on board a Falcon 9 – Rideshare Mission Transporter-12. “NextSpace” is the term legally reserved for exclusive use by Reflex to describe the new speed in the development, production and provision of space technology, coupled with innovative versatility as a leitmotif for the performance of the product.
To a large extent, this also applied to an essential element of the satellite not manufactured by Reflex: the core broadband reflector antenna developed by HPS from the medium-sized space technology company HPS GmbH (Munich, Germany) with a cavity-backed spiral antenna as an axial feed for a wide bandwidth and considerable gain – and all that from order to delivery in just 12 months.
HPS congratulates Reflex Aerospace on the first launch of one of its products and looks forward to working with them on further NextSpace challenges in space.
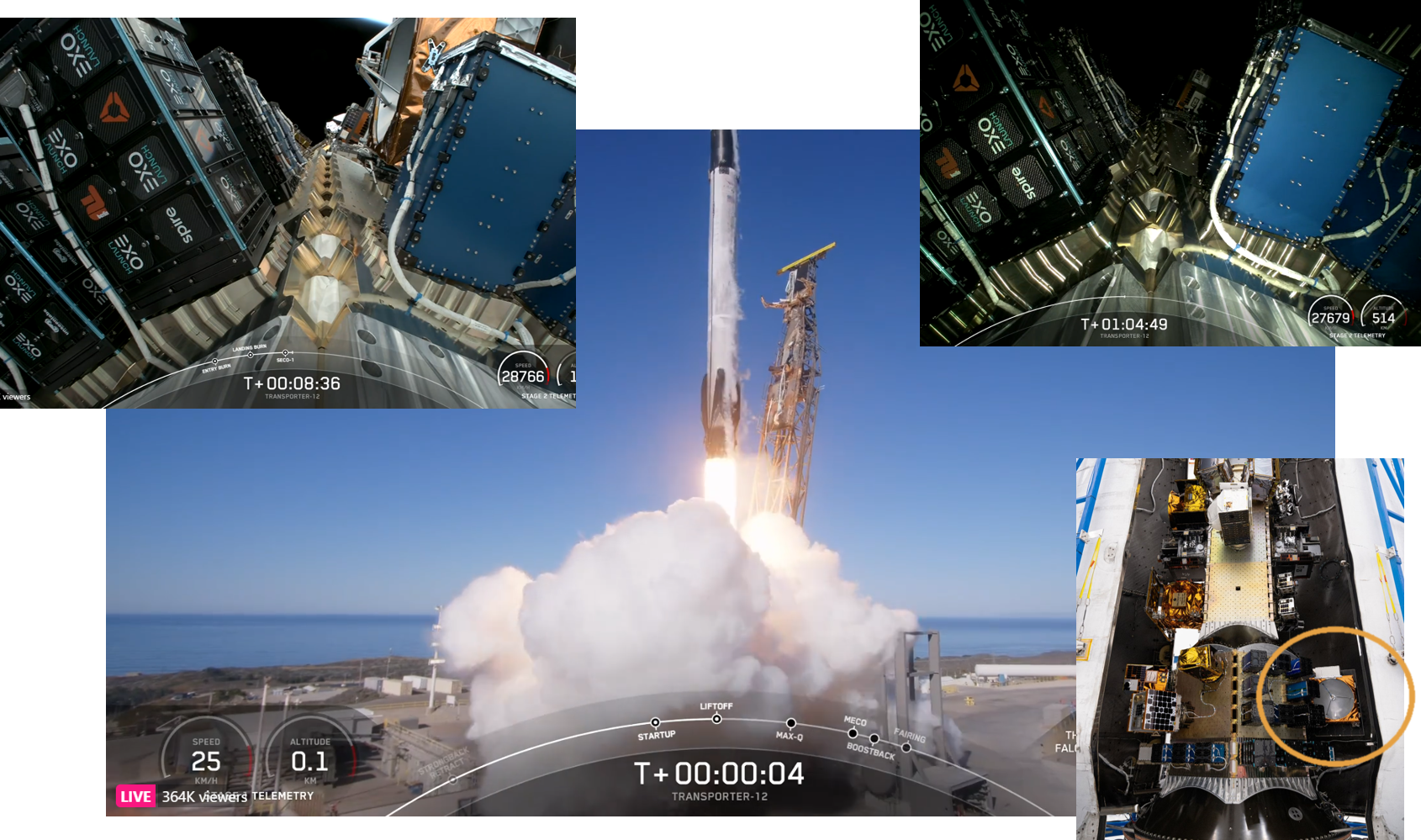
Pictures by SpaceX
Antenna specialist HPS conquers new territory in RF applications with verification of innovative 3D production
Even formerly very sceptical augurs of space travel now agree that the ability to largely automate the series production of lightweight components while minimizing raw materials and ensuring maximum reliability will have a significant impact on the future development of applicable technologies.
However, the central prerequisite for the implementation of such visions is still a very classic step-by-step verification, in this case of two materials selected by the HPS engineers using the new ESA standard ECSS-Q-ST-70-80C.
Given the future potential of such technology, the European and German space agencies have a primary interest in the success of the research at HPS and provided GSTP funding for the 3DPAN2 project: “3D-Printed Antenna 2” is a follow-up project to 3DPAN, which was completed five years ago and initially demonstrated the feasibility in principle of 3D-printed RF components.
The product objective was an extremely lightweight X-band antenna with a diameter of ~30cm for the data downlink of earth observation satellites. It was finally manufactured from the aluminum alloy SCALMALLOY at the sub-contractor APWORKS GmbH in Ottobrunn. In addition, a filigree feed support bracket made of titanium was manufactured for fold-out antennas by the long-standing HPS trusted partner, the Fraunhofer Institute for Material and Beam Technology IWS, Dresden, as a subcontractor.
Meanwhile, the respective designs and FE analyses, as well as their iterative optimization, were carried out by HPS in Munich itself.
The final tests delivered positive results that exceeded all expectations. This applied in particular to the RF performance of the X-band antenna in the Compensated Compact Range (Munich University of Applied Science MUAS). Resistance to vibration (sine + random) was also successfully demonstrated for both demonstrators at SGS GmbH, Geretsried: here too, everything went without complications, i.e. above all without damage or deformation. Even a final TVAC test (10 cycles between +120°C and – 120°C) showed no cracks or deformations on the demonstrators.
Olaf Stolz, the responsible project manager at HPS, summed up the project as follows: “The objectives of the verification processes were achieved without any restrictions: the additively manufactured demonstrators were 20% and 25% lighter than corresponding conventionally manufactured components – a well-known enormous advantage in space travel. There were no restrictions on qualification for space applications. We would like to thank our cooperation partners, especially Dr. Samira Gruber (Fraunhofer IWS) and Mr. Nicklas Schwab (APWORKS) for the extremely good and successful cooperation in the project, as well as ESA, in particular Ms. Isabel Olaya Leon, Technical Officer of the 3DPAN2 project.
HPS CEO Ernst K. Pfeiffer is delighted: “It is fantastic that we are already implementing 3D printed components with the technology results of the ESA GSTP program in current flight projects. A goal that we set 8 years ago and that is essential for the future market has now been achieved.”
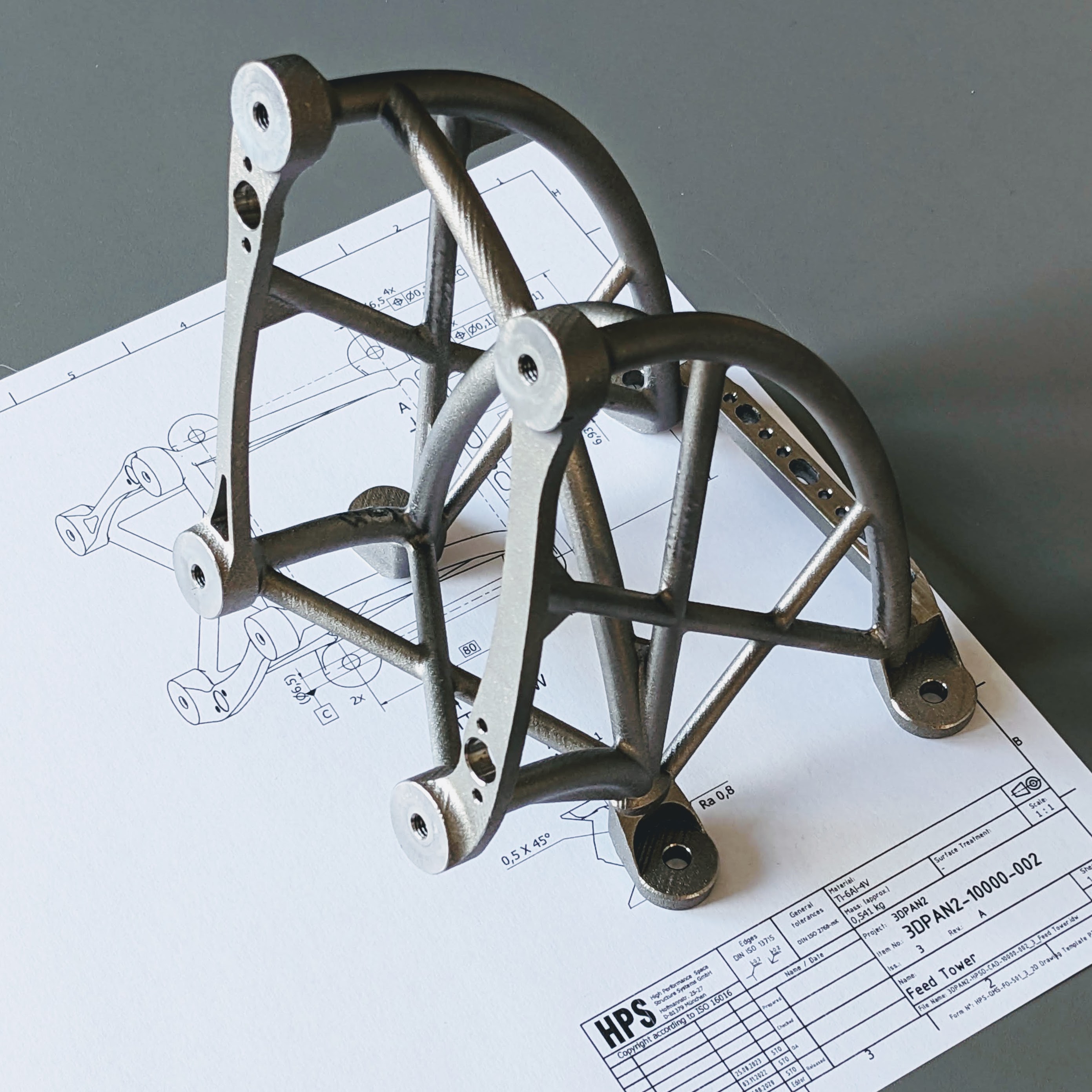
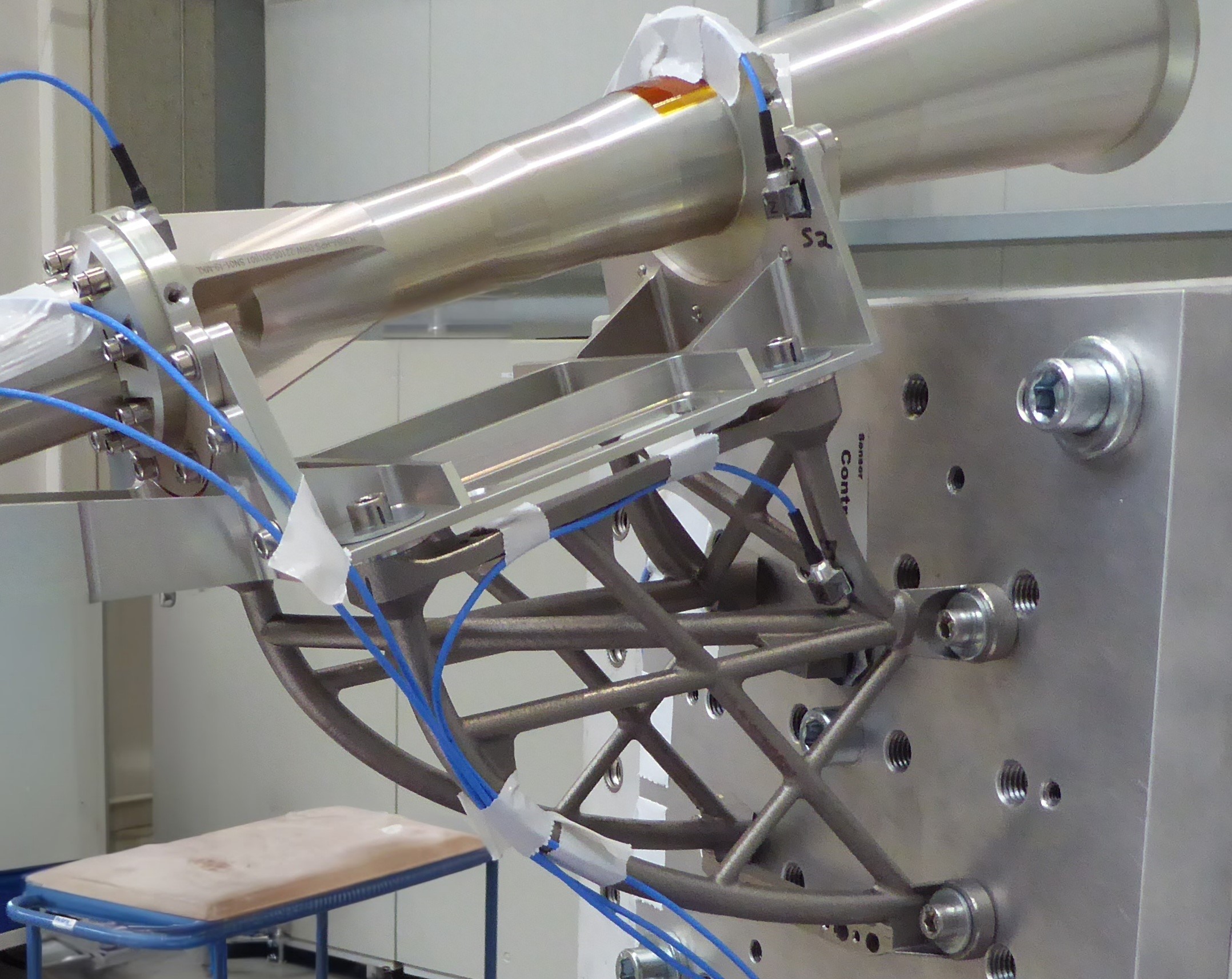
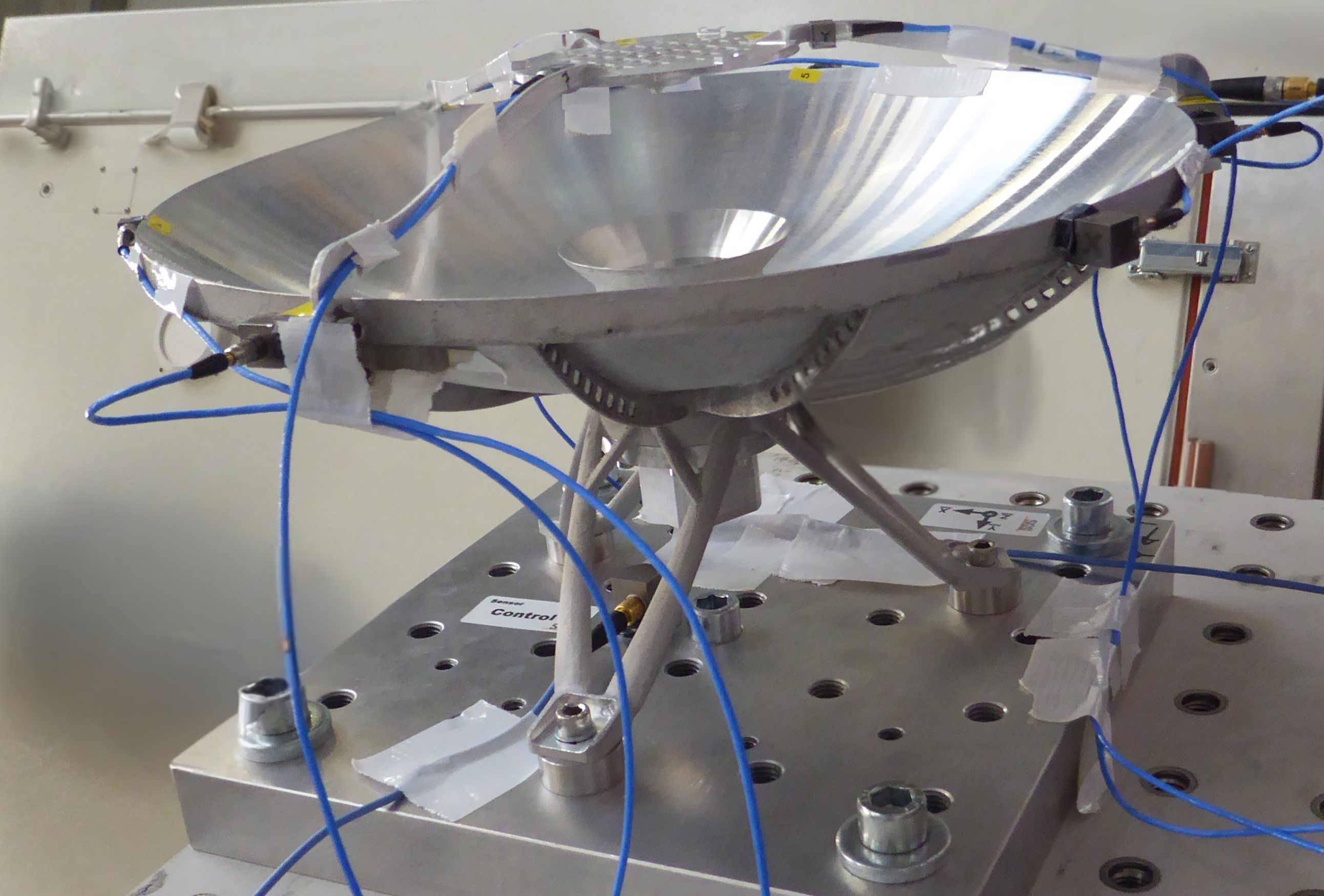
Producing antennas in series
For over 20 years, the Munich-based space technology company HPS has been known for breaking new ground wherever possible and establishing an increasingly solid bridge between ClassicSpace and CommercialSpace with innovations of all kinds. This applies to products such as deployable antennas of all sizes through to processes such as the series production of the deorbit sail module product family (ADEO).
With the implementation of a further process innovation, HPS is now also realizing new efficiency horizons in the antenna sector, because a commercial customer is in a hurry: more than 20 broadband antennas are needed, in a period of less than only 12 months, starting NOW. HPS is already known from a large number of successfully completed antenna orders – whether from the institutional or commercial sector – for the routine of quality production at a consistently high level that is valued by customers. But now, with the start of small series production, the company is heralding the introduction of a further development stage in the process of merging the quality features of conventional and new space technology into something new and even better. And despite all the high pressure, with the power that comes from calm.
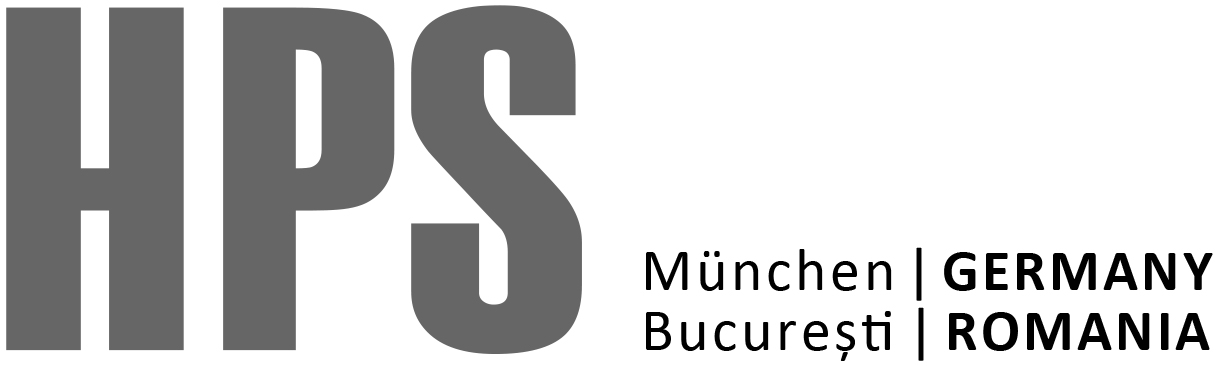